What does the reduced volume of a particular container signify, and why is it important?
The reduction in the volume of barrels, often used for storing liquids or goods, has various implications depending on the context. It can reflect a decrease in the amount of contents held within a container, potentially due to leakage, evaporation, or a change in the material state of the stored substance. For instance, a decrease in the volume of oil barrels may indicate a loss of product, or a reduction in the size of a product packaging container may signal a change in production. This measurement is important in inventory management, loss control, and for assessing potential environmental contamination or damage.
Understanding the reasons for reduced volume within storage containers is critical in many industries. This knowledge is fundamental in maintaining accurate inventory records, preventing significant product losses, and ensuring compliance with regulations. Monitoring the volume of contents within storage units over time can reveal patterns in loss or indicate potential issues in storage or transportation. Furthermore, historical records of such volume changes can serve as valuable data in analyzing the effectiveness of storage systems or the stability of the products themselves.
Let's now delve into the specific applications of this phenomenon within various sectors like oil, food, and environmental management.
Deflated Barrels
Understanding the condition of deflated barrels is crucial for various industries, affecting everything from inventory accuracy to environmental safety.
- Volume reduction
- Loss assessment
- Leak detection
- Product quality
- Storage integrity
- Regulatory compliance
Deflated barrels, indicating a reduction in volume, signal potential issues. Loss assessment becomes paramount, factoring in the volume difference for accurate inventory management. Leak detection is crucial for preventing further loss and environmental contamination. Product quality can be compromised if contents have degraded due to exposure or changes in temperature, leading to quality concerns. Storage integrity is compromised if barrels are visibly damaged or leaking. Finally, regulatory compliance often mandates regular monitoring and reporting of barrel contents, making accurate volume measurement essential. For example, in the oil industry, a deflated barrel may signify a leak, prompting immediate action to prevent environmental damage. Likewise, in food processing, a significant loss in volume may indicate product spoilage, necessitating corrective measures and potentially affecting quality control systems.
1. Volume Reduction
Volume reduction, a key indicator in assessing the state of storage containers, is inextricably linked to the condition of deflated barrels. The decrease in volume within these containers reveals critical information about product loss, potential leaks, and the overall integrity of the storage system. This analysis is crucial for industries dealing with liquids, gases, and commodities stored in bulk.
- Product Loss and Inventory Accuracy
A reduction in volume directly signifies a loss of product. This loss can stem from leakage, evaporation, or even physical damage. Accurate volume measurement is essential for maintaining accurate inventory records and financial accountability. For instance, significant volume loss in fuel storage tanks requires immediate investigation to pinpoint the cause and prevent further loss, leading to financial penalties or operational disruptions.
- Leak Detection and Prevention
Volume reduction often indicates a leak, necessitating immediate attention to prevent further loss and potential environmental contamination. Identifying the source of the leak, be it a damaged seal, a faulty valve, or a structural weakness in the barrel, is paramount. Early detection prevents escalating issues, potentially saving substantial resources and mitigating environmental risks.
- Material Degradation or Change in State
Changes in stored materials can also cause volume reduction. For example, evaporation of volatile substances or a change in the density of a material after storage, or changes from temperature or pressure differences, can cause a measurable decrease in volume. Analyzing such changes helps identify product deterioration or the need for adjustments in storage conditions.
- Storage System Integrity Assessment
Consistent volume reduction across multiple containers suggests a potential problem with the storage system itself. Issues with the container design, inadequate maintenance of the facilities, or improper handling procedures could be contributing factors. Systematic assessment of the storage system is essential to identify and address these underlying causes to ensure future storage integrity.
Understanding the relationship between volume reduction and the condition of deflated barrels is critical for effective inventory control, risk management, and compliance with regulations. Consistent monitoring and analysis of volume trends allow for proactive measures to be implemented, preventing further losses and safeguarding resources.
2. Loss Assessment
Loss assessment is integral to understanding the implications of deflated barrels. The reduction in volume within a barrel signifies a loss of contents, whether through leakage, evaporation, or other causes. Accurate loss assessment is crucial for determining the extent of the loss and for identifying the root cause. Without accurate assessment, a company may underestimate financial losses, mismanage inventory, and fail to address potential environmental hazards.
Consider a scenario in the oil industry. A series of deflated barrels indicates a leak in a pipeline or storage facility. Thorough loss assessment, encompassing the volume difference and analysis of potential leak sources, is vital. This assessment enables proactive measures to stop the leak, prevent further environmental contamination, and calculate financial losses associated with the incident. A similar situation could arise in a food processing plant, where deflated barrels of processed ingredients might indicate spoilage or contamination. Assessing the extent of spoilage and its possible impact on the product line is paramount for food safety and economic considerations. In both cases, loss assessment allows for corrective actions to be implemented, preventing future issues and maximizing resource utilization.
The importance of loss assessment in relation to deflated barrels transcends immediate financial concerns. It informs critical decisions related to regulatory compliance, safety protocols, and resource allocation. Accurate loss assessments empower organizations to respond swiftly and effectively to these situations, maintaining operational efficiency and public trust. Ultimately, a robust loss assessment process in the context of deflated barrels contributes significantly to the overall efficacy of a business and its commitment to environmental responsibility.
3. Leak Detection
Leak detection is a critical component in managing the condition of deflated barrels. Identifying the source of a leak is paramount for preventing further loss of contents, mitigating environmental damage, and ensuring regulatory compliance. The presence of deflated barrels often signals a leak, highlighting the need for immediate investigation and corrective action.
- Visual Inspection and Monitoring
Visual inspection of storage containers, including barrels, is a fundamental method for detecting leaks. Identifying any signs of fluid seepage, wet spots, or pooling around the barrels facilitates early detection. Regular monitoring can also reveal patterns suggestive of subtle leaks that may not be immediately apparent. For example, a gradual decline in the volume of a barrel over time may indicate a slow leak, requiring prompt attention.
- Pressure and Vacuum Measurement
Monitoring pressure and vacuum levels within storage systems, particularly applicable in cases involving pressurized liquids or gases, is crucial. Deviations from expected readings can indicate leaks or other issues within the system. For example, consistent drops in pressure in a container storing compressed gas directly point towards a potential leak, necessitating immediate investigation and repairs.
- Acoustic Monitoring
Acoustic techniques, such as listening for hissing or bubbling sounds, can detect subtle leaks, often undetectable through visual inspection alone. Specialized equipment can amplify these sounds, providing early warning signals for leakages. This method is particularly useful in situations with large storage areas, or when the leak might be concealed. For instance, leak detection using acoustic methods in underground storage tanks can aid in pinpointing the exact location of a leak, allowing for focused repairs and reduced environmental impact.
- Specialized Leak Detection Technologies
Advanced technologies, such as moisture sensors or tracer gas methods, can pinpoint leaks with high precision and speed. These methods can be especially effective in identifying smaller or more complex leaks in hard-to-reach or concealed areas. Implementing such technologies streamlines the leak detection process, helping pinpoint sources quickly for effective and prompt corrective actions. For example, specialized detectors can identify minuscule leaks of volatile liquids in storage facilities, preventing significant losses and minimizing potential environmental damage.
Effective leak detection strategies encompass a combination of methods tailored to the specific circumstances and materials involved. In cases involving deflated barrels, a multi-faceted approach employing visual, pressure/vacuum, and acoustic methods, along with potentially specialized technologies, will maximize the effectiveness and efficiency of the leak detection process, minimizing the overall impact of leakage. The implementation of well-designed and robust leak detection strategies in the context of deflated barrels is paramount for ensuring the integrity of stored materials and mitigating environmental damage.
4. Product Quality
Deflated barrels, signifying a reduction in volume, often indicate compromised product quality. The cause-and-effect relationship is multifaceted. Leakage, a frequent consequence of deflated barrels, leads to product loss and potential contamination. This contamination can result in compromised quality, affecting purity, freshness, or structural integrity, depending on the product. Evaporation or material degradation within the container can alter the product's characteristics, affecting its intended use and impacting quality metrics.
Consider a food processing facility storing barrels of fresh juice. Deflated barrels might indicate leaks allowing air and potentially contaminants to enter. This results in oxidation, microbial growth, and spoilage, leading to a decline in the juice's quality attributes like color, taste, and overall safety. In a pharmaceutical industry context, deflated barrels holding a critical medication could point to material degradation affecting the potency and efficacy of the drug, jeopardizing patient health. Similarly, in the chemical sector, a loss of volume in a barrel of a reagent could imply leakage or evaporation, compromising the purity and resulting in a product that no longer meets quality standards for intended use. These examples underscore the vital link between barrel condition and the end product's quality.
Understanding the connection between deflated barrels and product quality is crucial for preventative measures and quality control. Regular monitoring of barrel condition and prompt identification of leaks allow for swift containment and mitigation of damage. This proactive approach helps maintain product quality, minimize losses, and uphold standards throughout the supply chain. Ultimately, this knowledge supports efficient resource allocation, minimizes financial losses, and safeguards public safety.
5. Storage Integrity
Storage integrity, encompassing the structural soundness and operational efficiency of storage systems, is paramount for maintaining product quality, preventing loss, and ensuring regulatory compliance. Deflated barrels, indicative of compromised storage conditions, directly challenge storage integrity. Understanding the interconnectedness of these elements is essential for preventing broader issues.
- Structural Soundness of Containers
The integrity of the storage containers themselves is crucial. Defective barrels, showing signs of damage, leaks, or deterioration, compromise the overall system. This includes evaluating materials, ensuring proper seals, and addressing any manufacturing defects. Examples include rust-perforated barrels holding chemicals or cracks in the barrels storing food products. Such compromised integrity directly impacts product quality, potentially leading to contamination or loss.
- Maintenance and Handling Practices
Proper maintenance and handling procedures are critical. Regular inspections, appropriate storage environments (temperature, humidity), and safe handling techniques mitigate risks. Neglecting these practices can lead to corrosion, deterioration, or damage over time. Examples include insufficient cleaning of storage tanks, improper stacking of barrels leading to damage, or failure to routinely inspect seal integrity, all potentially contributing to deflated barrels.
- Environmental Factors and Storage Conditions
Environmental factors can significantly affect storage integrity. Temperature fluctuations, moisture exposure, and exposure to corrosive substances weaken containers and lead to internal pressure changes and subsequent leaks. The long-term stability of the product is also affected, directly contributing to reduced volume. Examples include improper climate control, storing containers outdoors in wet conditions or near high-temperature sources, all impacting storage longevity and causing deflated barrels.
- Design and System Optimization
The overall design and optimization of the storage system play a critical role. Well-designed systems minimize environmental exposures, ensure robust container materials, and incorporate leak detection mechanisms. Examples include well-insulated tanks, advanced sealing systems, and robust monitoring procedures. A poorly-designed system will have a higher likelihood of compromised integrity over time, which is directly associated with the emergence of deflated barrels.
In conclusion, ensuring the integrity of the storage systemincluding the containers, practices, conditions, and designis critical in maintaining the quality and safety of stored products. Compromised storage integrity, manifested in deflated barrels, signals a potential for product loss, contamination, and costly damage. Proactive monitoring, preventative maintenance, and a focus on sound storage design are all critical elements in avoiding these outcomes.
6. Regulatory Compliance
Regulatory compliance plays a critical role in mitigating risks associated with deflated barrels. Standards and regulations exist to ensure safe handling, storage, and disposal of various materials, including those stored within barrels. Non-compliance can lead to significant penalties, environmental damage, and reputational harm. Understanding the specific regulations pertinent to deflated barrels is crucial for preventing issues and upholding legal standards.
- Inventory Management and Record-Keeping
Regulations often mandate meticulous record-keeping of stored materials. This includes detailed documentation of initial volumes, any observed decreases (deflated barrels), and the reasons for such reductions. Properly documented records provide evidence of compliance and aid in tracing the source of volume loss, facilitating timely remedial actions and minimizing liabilities. Accurate inventory tracking is paramount, particularly in industries with strict regulatory oversight, ensuring complete accountability and the ability to quickly identify irregularities.
- Environmental Protection Standards
Regulations concerning environmental protection dictate the management of potentially hazardous materials stored within barrels. Leaks, spills, or evaporation leading to deflated barrels can cause significant contamination. Non-compliance with environmental standards can result in fines, remediation costs, and damage to public health and ecosystems. These standards frequently require measures like containment systems, leak detection methods, and specific procedures for handling contaminated materials, all contributing to a robust environmental safety framework surrounding deflated barrels.
- Safety Protocols and Procedures
Safety regulations often govern the handling, transport, and storage of materials within barrels. Procedures and protocols are put in place to prevent accidents and minimize the risk of damage or leaks related to deflated barrels. This includes establishing secure storage areas, using proper handling equipment, and training personnel on safety procedures. Compliance with these safety protocols is critical to prevent incidents that could lead to employee injuries, environmental contamination, and financial penalties.
- Specific Industry Regulations
Specific industries like oil and gas, chemicals, and food processing have unique regulatory frameworks regarding deflated barrels. These frameworks often establish stricter standards based on the inherent risks associated with the specific materials handled. Industries must adhere to these regulations to safeguard both workers and the environment from potential hazards associated with defective barrels or leaks. For example, oil and gas companies might face specific guidelines concerning leak detection and containment procedures for deflated barrels.
In summary, regulatory compliance is fundamental in addressing the potential consequences of deflated barrels. Adherence to relevant standards and regulations enables businesses to manage risks, protect the environment, and maintain safe operational practices. A comprehensive approach incorporating inventory management, environmental protection, safety protocols, and specific industry regulations is crucial for navigating the complexities surrounding deflated barrels and demonstrating commitment to responsible business practices.
Frequently Asked Questions about Deflated Barrels
This section addresses common questions and concerns regarding deflated barrels, offering concise and informative answers. Understanding the causes, implications, and appropriate responses to deflated barrels is crucial for maintaining safe and compliant operations.
Question 1: What are the primary causes of deflated barrels?
Deflated barrels often indicate a loss of volume within the container. Common causes include leaks (punctures, damaged seals, or faulty valves), evaporation of volatile contents, changes in the physical state of the stored material (e.g., shrinking of liquids under differing temperature conditions), and in some cases, structural failure of the barrel itself.
Question 2: What are the immediate actions required when encountering deflated barrels?
Immediate action depends on the context but generally involves isolating the affected area, containing any potential leaks to prevent environmental contamination, and initiating an investigation into the cause. Identifying the type of material stored is crucial for determining appropriate containment procedures. If personnel safety is at risk, evacuation may be necessary. Contacting relevant authorities and safety personnel may be required, especially if the material poses a significant environmental or health hazard.
Question 3: How can the potential consequences of deflated barrels be mitigated?
Mitigation strategies encompass preventing leaks through rigorous inspection of storage facilities, utilizing proper handling procedures, and implementing regular maintenance schedules for equipment and containers. Early detection methods, such as pressure sensors and visual monitoring, assist in identifying potential problems promptly. Effective inventory management systems track material levels and facilitate rapid identification of volume discrepancies. Implementing containment strategies and conducting proper waste disposal are also important.
Question 4: What records should be maintained regarding deflated barrels?
Comprehensive records are critical for tracking and managing deflated barrels. This includes dates of observation, the volume of material loss, potential causes identified during investigation, any environmental incidents resulting from the deflated barrels, and corrective actions undertaken. Such records provide a historical perspective for future evaluations, assist in risk assessments, and aid in demonstrating compliance with regulations.
Question 5: What regulatory guidelines are relevant to deflated barrels?
Regulatory guidelines regarding deflated barrels vary depending on the material being stored and the relevant jurisdiction. These guidelines typically cover issues such as safety protocols for handling hazardous materials, environmental protection standards (e.g., spill prevention and containment), and record-keeping requirements. Consulting relevant authorities and regulatory documents specific to the industry and location will clarify applicable guidelines.
Understanding the causes, consequences, and mitigation strategies related to deflated barrels is essential for maintaining safe and compliant operations. Thorough documentation, proactive maintenance, and adherence to regulatory guidelines are crucial elements in preventing further issues.
Transition to the next section on specific storage practices for different types of materials.
Conclusion
The examination of deflated barrels reveals a multifaceted issue impacting various sectors. Reduced volume within storage containers signals potential product loss, leakage, and compromised storage integrity. Accurate loss assessment, coupled with effective leak detection strategies, is crucial for mitigating financial and environmental risks. Furthermore, adherence to relevant regulatory guidelines and proactive maintenance practices are paramount for preventing further incidents. Understanding the interplay between product quality, storage integrity, and regulatory compliance is essential for establishing robust safeguards against potential issues stemming from deflated barrels. The consequences of neglecting these aspects can range from significant financial losses to severe environmental damage and compromised public safety.
The importance of preventative measures cannot be overstated. Implementing robust monitoring systems, conducting regular inspections, and prioritizing maintenance are crucial steps in preventing deflated barrels. Furthermore, cultivating a culture of safety and compliance, integrating thorough record-keeping practices, and fostering a proactive approach to identifying and addressing potential issues are critical to long-term operational stability and environmental responsibility. A holistic strategy encompassing these elements is vital to minimizing the impact of deflated barrels and maintaining the integrity of stored materials across diverse industries.
You Might Also Like
Secret DM Tips: Slide Into Their DMs Like A Pro!Elvis Presley & Priscilla: Marriage Age Difference Revealed
Top Female CNN Anchors: News & Expertise
Bleach Bount Arc Episodes: All You Need To Know!
Stunning Asian Playboy Playmates: Photos & Videos
Article Recommendations
- Unveiling The Life Of Jacklyn Gise A Comprehensive Insight
- The Comprehensive Guide To Sustainability Laws Regulations Frameworks And Compliance
- Megan Fox Mom A Glimpse Into The Life Of A Hollywood Icon And Her Family
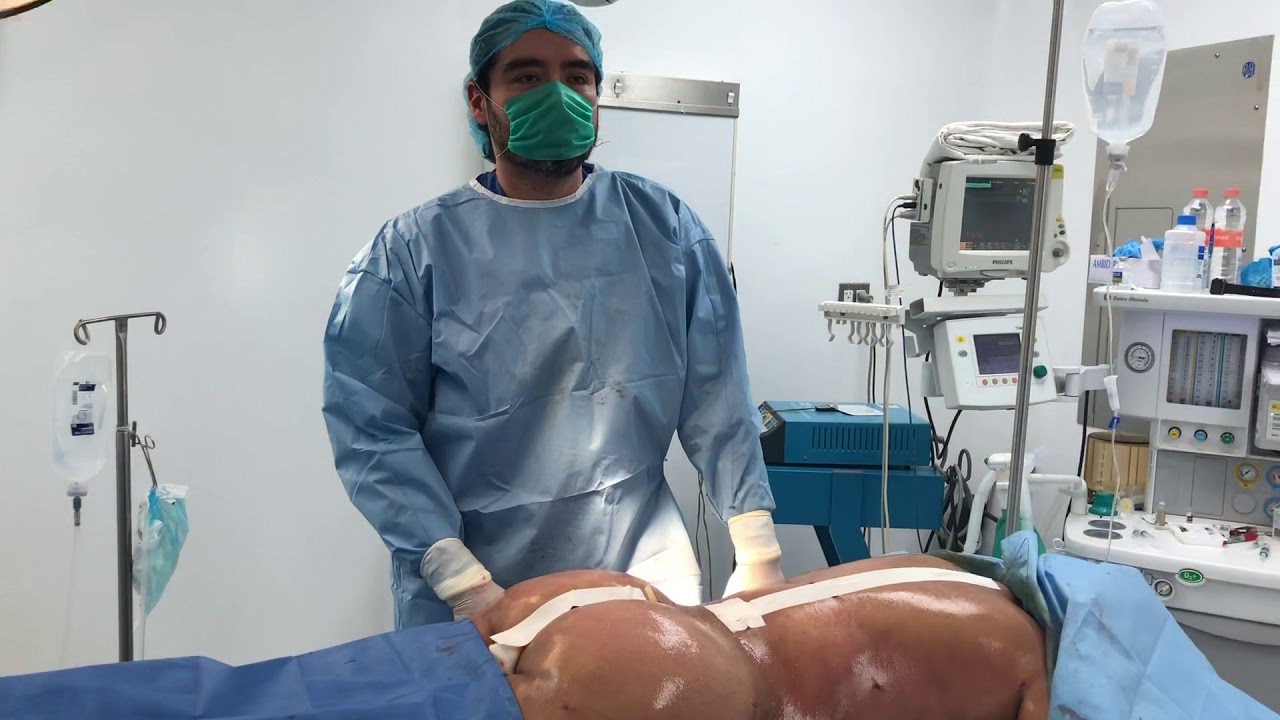

