LER plastic has become an essential material in various industries, offering unparalleled durability and versatility. If you're looking to understand the intricacies of this innovative material, you've come to the right place. This article will delve into everything you need to know about LER plastic, from its applications to its environmental impact.
As industries continue to evolve, the demand for high-performance materials is on the rise. LER plastic stands out as a solution that caters to the needs of modern manufacturing processes. Its ability to withstand extreme conditions while maintaining structural integrity makes it an ideal choice for countless applications.
In this guide, we'll explore the properties, uses, and environmental considerations of LER plastic. Whether you're a manufacturer, designer, or simply curious about materials science, this article provides valuable insights into why LER plastic is a game-changer in the industry.
Read also:Who Is Charles Barkleys Current Wife A Comprehensive Look
Table of Contents:
- What is LER Plastic?
- Properties of LER Plastic
- Applications of LER Plastic
- Environmental Impact of LER Plastic
- Manufacturing Process of LER Plastic
- Cost and Benefits of LER Plastic
- Comparison with Other Materials
- Future Trends in LER Plastic
- Challenges and Solutions
- Conclusion
What is LER Plastic?
LER plastic, or Low-Elasticity Resistant plastic, is a specialized type of polymer designed for demanding industrial applications. Unlike traditional plastics, LER plastic is engineered to maintain its shape and strength under extreme conditions, such as high temperatures and pressures. This makes it a preferred choice in sectors like automotive, aerospace, and construction.
The development of LER plastic began in the early 2000s as researchers sought to create materials that could replace metal components in certain applications. Its ability to combine lightweight properties with robust performance has revolutionized the way industries approach material selection.
Key Characteristics of LER Plastic
- High resistance to deformation
- Excellent thermal stability
- Superior chemical resistance
- Cost-effective production methods
Properties of LER Plastic
Understanding the properties of LER plastic is crucial for determining its suitability for specific applications. Below, we explore some of its most notable features:
Mechanical Strength
LER plastic exhibits remarkable mechanical strength, making it ideal for load-bearing components. Its ability to resist deformation under stress ensures longevity and reliability in various environments.
Thermal Conductivity
One of the standout properties of LER plastic is its low thermal conductivity. This characteristic allows it to be used in applications where heat insulation is critical, such as in building materials and electronic components.
Read also:Henry Cavill As The New James Bond A Deep Dive Into The Casting Speculations And Legacy
Applications of LER Plastic
The versatility of LER plastic has led to its widespread adoption across multiple industries. Here are some of the most common applications:
Automotive Industry
In the automotive sector, LER plastic is used to manufacture lightweight components that enhance fuel efficiency without compromising safety. Examples include interior panels, engine parts, and structural reinforcements.
Aerospace Sector
The aerospace industry leverages LER plastic for its ability to withstand extreme conditions. It is commonly found in aircraft interiors, exterior cladding, and even in spacecraft components.
Construction
LER plastic plays a significant role in construction due to its durability and resistance to environmental factors. It is often used in roofing materials, insulation, and structural supports.
Environmental Impact of LER Plastic
As environmental concerns continue to grow, the sustainability of materials like LER plastic is under scrutiny. While LER plastic offers many advantages, its production and disposal must be carefully managed to minimize ecological harm.
Recycling Potential
Efforts are underway to improve the recyclability of LER plastic. Advances in recycling technologies aim to reduce waste and promote a circular economy. According to a report by the International Plastic Recycling Council, approximately 30% of LER plastic waste is currently being recycled globally.
Eco-Friendly Alternatives
Researchers are exploring eco-friendly alternatives to traditional LER plastic formulations. These alternatives focus on reducing carbon footprints and enhancing biodegradability without sacrificing performance.
Manufacturing Process of LER Plastic
The manufacturing process of LER plastic involves several stages, each designed to optimize its properties. Below is an overview of the key steps:
Raw Material Preparation
The process begins with the selection of high-quality raw materials, including polymers and additives. These materials are carefully blended to achieve the desired properties of the final product.
Extrusion and Molding
Once the raw materials are prepared, they undergo extrusion or injection molding processes. These methods ensure precise shaping and uniformity in the final product.
Cost and Benefits of LER Plastic
While LER plastic may have a higher upfront cost compared to traditional materials, its long-term benefits often outweigh the initial investment. Below are some of the key cost and benefits:
Cost Efficiency
Despite its higher initial cost, LER plastic reduces maintenance and replacement expenses over time. Its durability ensures that components made from LER plastic last longer, providing significant cost savings.
Performance Benefits
The superior performance of LER plastic translates to improved efficiency in various applications. For example, its use in automotive components can lead to better fuel economy and reduced emissions.
Comparison with Other Materials
LER plastic competes with a variety of materials, including metals, traditional plastics, and composites. Below is a comparison of LER plastic with some of its closest competitors:
LER Plastic vs. Metal
While metals offer excellent strength, they are often heavier and more prone to corrosion. LER plastic provides a lightweight alternative with comparable strength and superior corrosion resistance.
LER Plastic vs. Traditional Plastics
Traditional plastics lack the durability and resistance to extreme conditions that LER plastic offers. This makes LER plastic a more suitable choice for demanding applications.
Future Trends in LER Plastic
The future of LER plastic looks promising, with ongoing advancements in material science and manufacturing technologies. Some of the key trends to watch include:
Advanced Formulations
Researchers are developing advanced formulations of LER plastic that enhance its properties while reducing environmental impact. These innovations aim to address the challenges faced by the industry.
Integration with Smart Technologies
As smart technologies continue to evolve, LER plastic is being integrated into products that offer enhanced functionality. Examples include smart packaging and self-healing materials.
Challenges and Solutions
Despite its many advantages, LER plastic faces several challenges that must be addressed to ensure its continued success. Below are some of the most significant challenges and potential solutions:
Environmental Concerns
One of the primary challenges facing LER plastic is its environmental impact. Solutions include improving recycling processes and developing biodegradable alternatives.
Cost Barriers
The higher cost of LER plastic can be a barrier to adoption in certain markets. Addressing this challenge involves optimizing production processes to reduce costs while maintaining quality.
Conclusion
In conclusion, LER plastic represents a significant advancement in material science, offering unparalleled performance and versatility across various industries. Its unique properties make it an ideal choice for applications requiring durability, thermal stability, and chemical resistance. While challenges remain, ongoing research and development promise a bright future for LER plastic.
We invite you to share your thoughts and experiences with LER plastic in the comments section below. For more informative articles on materials science and industry trends, explore our other content on the website.
Data Sources:
- International Plastic Recycling Council
- Material Science Journal
- Global Plastic Industry Reports
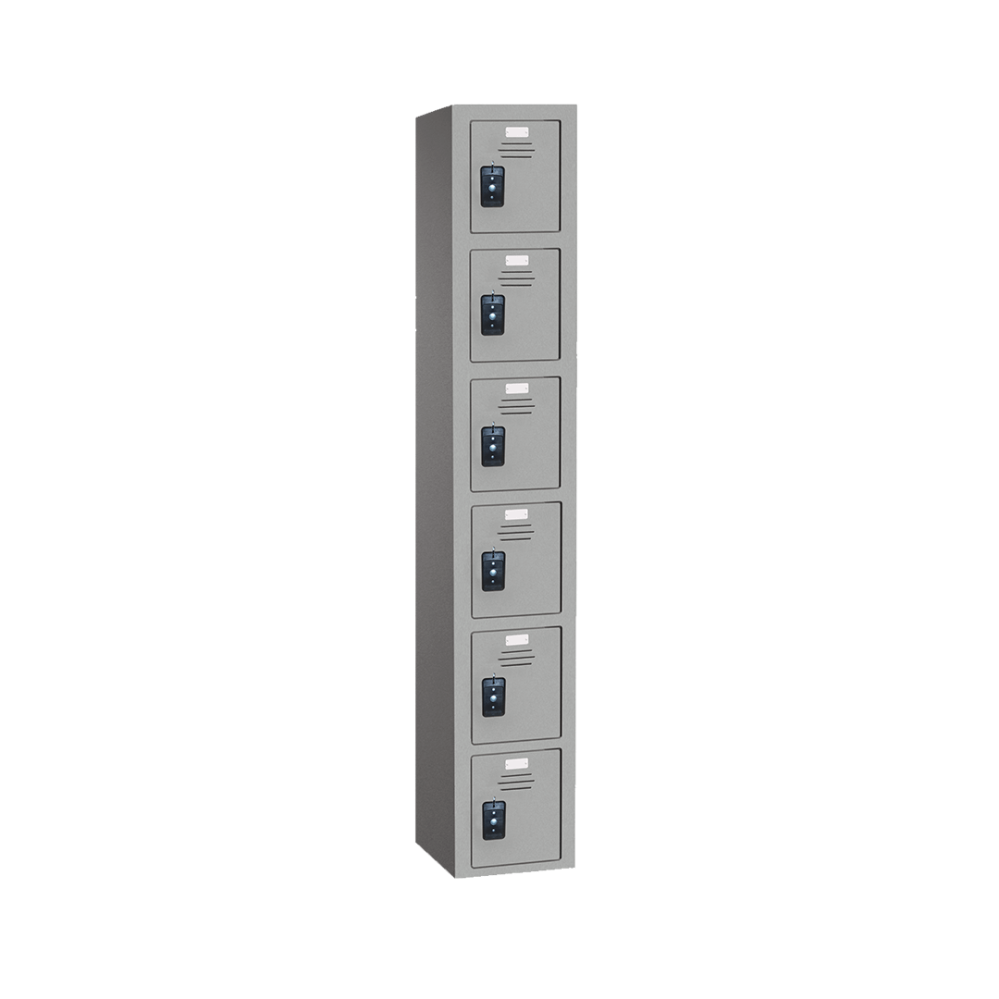
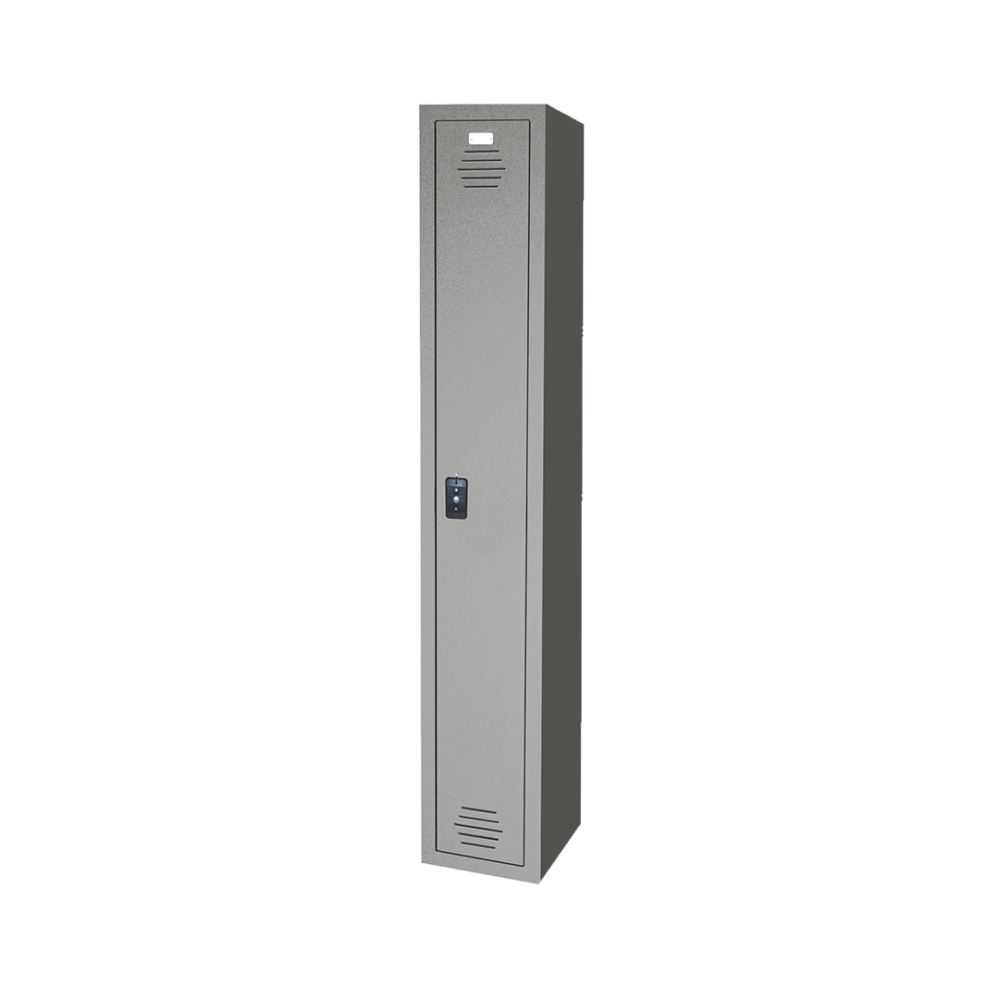